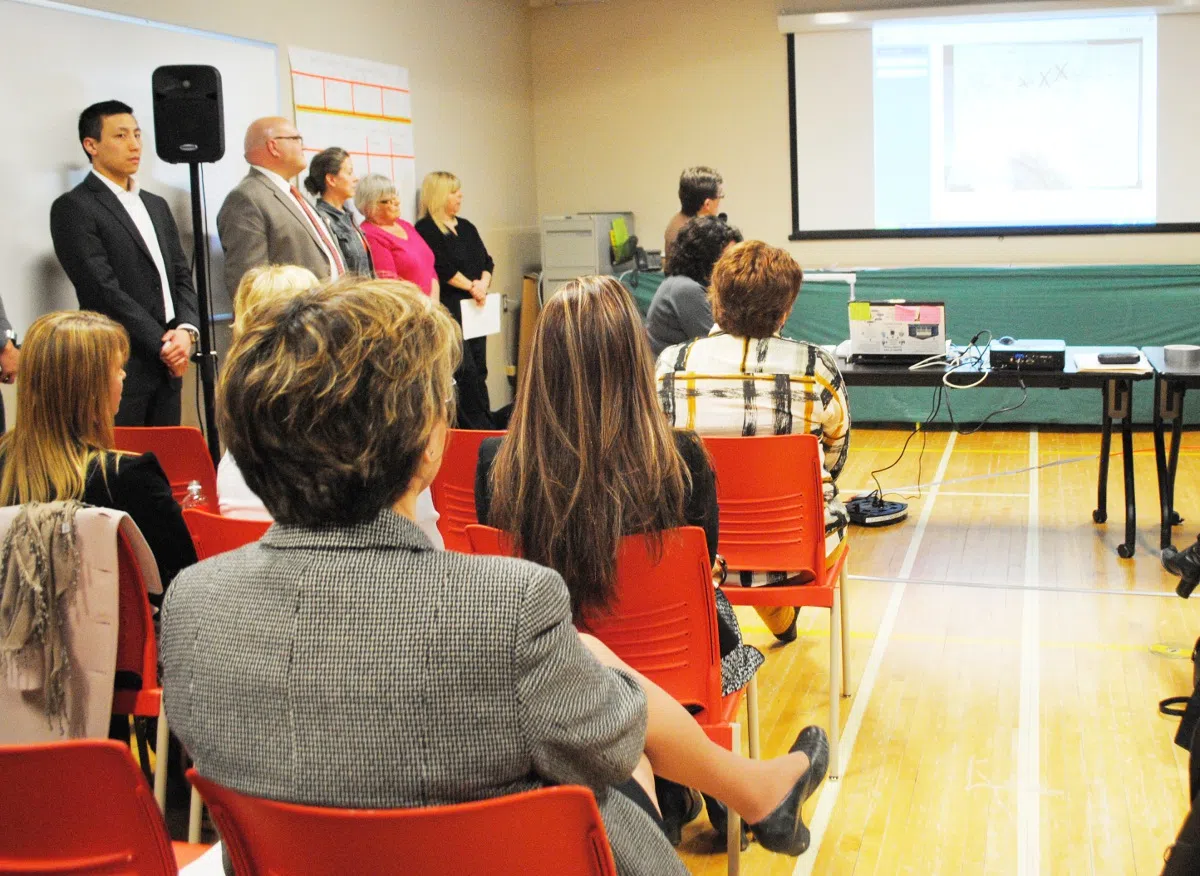
1 year of Lean management at the Victoria Hospital
Two Rapid Process Improvement Workshops (RPIW) have caused some changes in the surgery and Therapies Outpatient departments at the Victoria Hospital in hopes of making them more efficient.
On Friday afternoon the results, made through the provincial initiative of Lean management, were presented showing changes that affect wait-times and overtime.
The meeting comes weeks after the Lean project in Saskatchewan was put in the spotlight by NDP at the provincial legislature.
Cam Broten, Leader of Saskatchewan's NDP and MLA for Saskatoon-Massey Place said spending has gone over the top.